See This Report about Alcast Company
Alcast Company Can Be Fun For Everyone
Table of ContentsAn Unbiased View of Alcast CompanyThe Single Strategy To Use For Alcast CompanySome Known Questions About Alcast Company.Alcast Company for DummiesThe Single Strategy To Use For Alcast CompanyThe Best Guide To Alcast Company
The refined distinction depends on the chemical content. Chemical Contrast of Cast Aluminum Alloys Silicon promotes castability by lowering the alloy's melting temperature and improving fluidness during casting. It plays an important role in allowing detailed mold and mildews to be filled up accurately. Furthermore, silicon adds to the alloy's stamina and wear resistance, making it important in applications where toughness is critical, such as auto parts and engine components.It additionally enhances the machinability of the alloy, making it easier to refine right into ended up items. By doing this, iron adds to the overall workability of light weight aluminum alloys. Copper boosts electrical conductivity, making it useful in electric applications. It additionally enhances rust resistance and includes in the alloy's overall stamina.
Manganese contributes to the strength of aluminum alloys and improves workability. Magnesium is a lightweight component that gives strength and influence resistance to aluminum alloys.
The 20-Second Trick For Alcast Company
It allows the production of light-weight components with outstanding mechanical residential or commercial properties. Zinc enhances the castability of light weight aluminum alloys and assists manage the solidification procedure throughout spreading. It boosts the alloy's toughness and firmness. It is typically discovered in applications where intricate forms and fine details are required, such as decorative spreadings and certain auto parts.
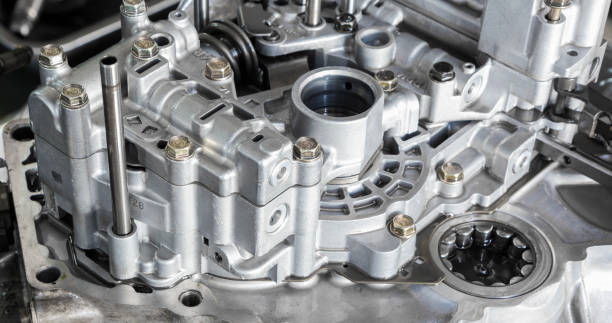
The primary thermal conductivity, tensile stamina, yield strength, and elongation differ. Select appropriate resources according to the efficiency of the target item generated. Among the above alloys, A356 has the highest possible thermal conductivity, and A380 and ADC12 have the most affordable. The tensile restriction is the contrary. A360 has the very best yield toughness and the highest possible elongation rate.
The Greatest Guide To Alcast Company

In accuracy spreading, 6063 is well-suited for applications where detailed geometries and high-grade surface finishes are paramount. Examples consist of telecommunication rooms, where the alloy's superior formability enables streamlined and cosmetically pleasing designs while maintaining architectural honesty. In the Lights Solutions industry, precision-cast 6063 components develop sophisticated and efficient lights components that require intricate forms and good thermal efficiency.
The A360 displays exceptional elongation, making it perfect for facility and thin-walled parts. In accuracy casting applications, A360 is well-suited for markets such as Customer Electronics, Telecommunication, and Power Devices.
The Definitive Guide for Alcast Company
Its special properties make A360 an important selection for precision casting in these industries, boosting item toughness and quality. Aluminum Casting. Light weight aluminum alloy 380, or A380, is a widely utilized casting alloy with a number of distinct characteristics.
In accuracy casting, aluminum 413 shines in the Consumer Electronic Devices and Power Equipment industries. It's commonly used to craft complex parts like smart device real estates, video camera bodies, and power tool coverings. Its accuracy is impressive, with tight resistances up to 0.01 mm, guaranteeing remarkable item setting up. This alloy's superior rust resistance makes it an excellent option for outside applications, guaranteeing lasting, resilient products in the stated sectors.
The Of Alcast Company
As soon as you have determined that the light weight aluminum die casting process is ideal for your task, a vital next step is selecting one of the most appropriate alloy. The light weight aluminum alloy you pick will considerably affect both the spreading process and the homes of the last product. Due to this, you have to make your decision meticulously and take an enlightened strategy.
Figuring out the most ideal aluminum alloy for your application will certainly suggest weighing a broad variety of features. These relative alloy attributes follow the North American Die Spreading Organization's standards, and we've separated them right into two classifications. The first group addresses alloy features that affect the manufacturing process. The 2nd covers attributes influencing the buildings of the end product.
Some Known Questions About Alcast Company.
The alloy you pick for die casting directly impacts a number of facets of the casting process, like exactly how easy the alloy is to function with and if it is vulnerable to casting problems. Hot cracking, likewise understood as solidification cracking, is a normal die spreading defect for light weight aluminum alloys that can lead to interior or surface-level rips or cracks.
Specific aluminum alloys are much more prone to hot breaking than others, and your choice must consider this. It can damage both the actors and the die, so you need to look for alloys with high anti-soldering homes.
Rust resistance, which is already a significant characteristic of aluminum, can differ substantially from alloy to alloy and is a necessary particular to think about relying on the ecological problems your item will certainly be exposed to (Aluminum Casting). Wear resistance is another building generally looked for in light weight aluminum products and can differentiate some alloys